Learning
The Essential Guide to Mining Conveyor Belts
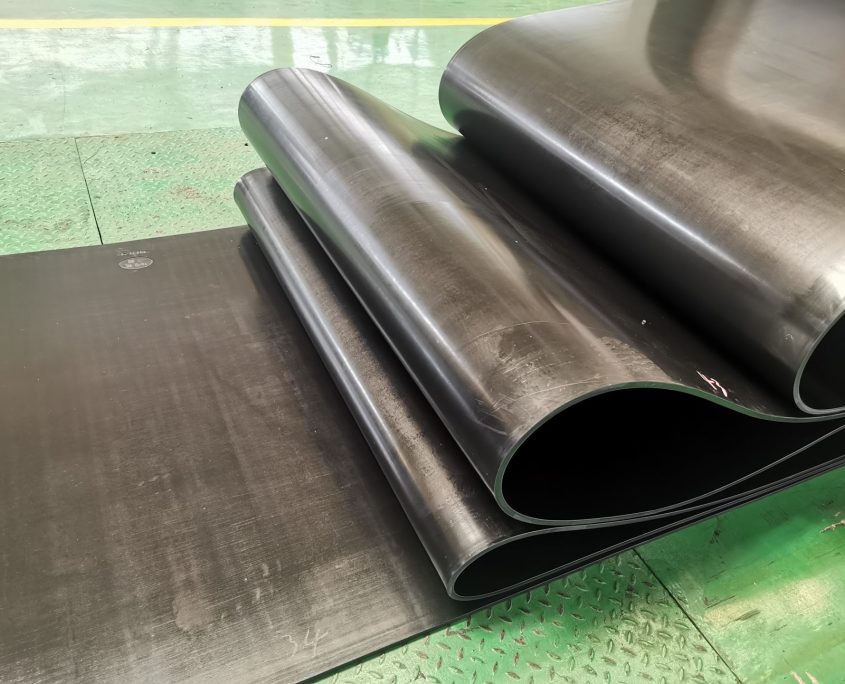
Learn about mining conveyor belts, their roles in operations, key components, and maintenance needs.
A mining conveyor belt is a specialized belt used in the mining industry to transport extracted minerals and ores. These belts, made from robust materials, are crucial for efficient material transport, cost reduction, enhanced safety, and operational efficiency. They are customizable to meet specific mining conditions and help reduce environmental impact.
Key components include the top layer, carcass, and bottom cover, each playing a significant role in the belt’s durability and performance. Understanding the different types of conveyor belts, such as multi-ply, straight-warp, steel-cord, solid woven, heat-resistant, and nylon conveyor belts, is essential for maintaining optimal performance and ensuring longevity.
What is a Mining Conveyor Belt?
Definition
A mining conveyor belt is a specialized belt designed specifically for use in the mining industry. It is engineered to transport extracted minerals and ores, such as coal, metals, and other mined materials, from the mining site to processing facilities, storage areas, or transportation hubs. These belts are constructed from robust materials that can withstand the harsh conditions of mining environments, including heavy loads, abrasive substances, and extreme temperatures.
Role in Mining Operations
The role of a mining conveyor belt in mining operations is multifaceted and crucial for the efficiency, safety, and productivity of the mining process. Here are the key functions and benefits:
- Efficient Material Transport:
- Mining conveyor belts streamline the transportation of extracted materials, ensuring a continuous and automated flow from the mining face (the active mining area) to various stages of processing and storage. This reduces the reliance on manual labor and increases overall productivity.
- Cost Reduction:
- By providing a reliable means of moving large quantities of materials over long distances and through challenging terrains, conveyor belts significantly lower operational costs. They minimize the need for multiple transport vehicles and reduce fuel consumption, labor costs, and maintenance expenses associated with other transportation methods.
- Enhanced Safety:
- Conveyor belts contribute to a safer working environment by reducing the risk of accidents associated with manual material handling. They are designed to handle hazardous conditions, such as fire and explosion risks in coal mining, with features like flame-resistant materials and robust construction.
- Operational Efficiency:
- The use of conveyor belts ensures a steady and controlled flow of materials, which helps maintain consistent production rates. This minimizes downtime and interruptions in the mining process, leading to more efficient operations and higher output.
- Adaptability to Mining Conditions:
- Mining conveyor belts are customizable to meet the specific needs of different mining environments. Whether it’s navigating steep inclines in underground mines or enduring extreme weather conditions in surface mining, these belts can be tailored in terms of size, material composition, and design features to handle various challenges.
- Environmental Impact:
- Conveyor belts can positively impact the environment by reducing the carbon footprint associated with material transport. Their energy-efficient designs and ability to operate with minimal emissions contribute to more sustainable mining practices.
- Compliance with Regulations:
- Utilizing conveyor belts that meet industry standards and safety regulations ensures that mining operations are compliant with legal requirements. This helps avoid fines and penalties, maintain a good industry reputation, and protect workers and equipment.
Key Components of a Conveyor Belt
A conveyor belt, particularly in mining operations, is composed of several key components that work together to ensure its strength, durability, and efficiency. Understanding these components is crucial for selecting the right belt for specific applications and for maintaining optimal performance in mining operations. The three primary components are the top layer, carcass, and bottom cover. A steel cord conveyor belt, for instance, uses steel cords in its carcass, providing exceptional tensile strength and durability, making it ideal for heavy-duty applications and long-distance transportation in mining environments.
Top Layer
Definition: The top layer, also known as the top cover, is the outermost part of the conveyor belt that comes into direct contact with the materials being transported.
Material Composition:
- The top layer is typically made from high-quality rubber compounds or synthetic materials such as PVC (polyvinyl chloride) or polyurethane.
- Flame-resistant materials are often used, especially in mining operations involving coal, to prevent fire hazards.
Functions:
- Wear Resistance: The top layer is designed to withstand the abrasion and wear caused by the transported materials. This is especially important in mining, where materials like coal, ores, and rocks can be highly abrasive.
- Impact Resistance: It absorbs the impact of heavy and sharp objects, preventing damage to the belt.
- Chemical Resistance: In some mining environments, the top layer must resist chemical exposure from the transported materials or the working environment.
Carcass
Definition: The carcass is the middle layer of the conveyor belt, providing structural support and strength. It is the backbone of the belt, determining its load-carrying capacity and durability.
Material Composition:
- The carcass can be made from various materials, including polyester, nylon, steel cords, or a combination of these.
- Multi-ply fabrics are also commonly used, where layers of fabric are bonded together for added strength.
Functions:
- Tensile Strength: The carcass provides the necessary tensile strength to handle heavy loads without stretching or breaking. High tensile strength is crucial for transporting large quantities of materials over long distances.
- Flexibility: Despite its strength, the carcass must be flexible enough to navigate complex paths, including inclines, declines, and curves. This flexibility ensures a smooth and continuous flow of materials.
- Load Support: The carcass supports the weight of the transported materials and helps distribute the load evenly across the belt, preventing sagging and maintaining operational efficiency.
Bottom Cover
Definition: The bottom cover is the underside layer of the conveyor belt that comes into contact with the conveyor system’s rollers and pulleys.
Material Composition:
- Like the top layer, the bottom cover is typically made from durable rubber compounds or synthetic materials such as PVC.
- It may also include reinforcement materials to enhance its strength and durability.
Functions:
- Friction Reduction: The bottom cover is designed to reduce friction between the belt and the conveyor components, ensuring smooth movement and minimizing wear on both the belt and the system.
- Protection: It protects the carcass from damage caused by contact with rollers, pulleys, and other conveyor parts. This protection extends the lifespan of the belt and reduces maintenance costs.
- Heat Resistance: In some applications, the bottom cover must withstand high temperatures generated by the conveyor system or the transported materials. Heat-resistant materials are used to maintain performance and prevent degradation.
Importance of These Components
Interconnected Functions:
- Each component of the conveyor belt works in conjunction with the others to ensure the overall performance and longevity of the belt. For example, while the top layer handles abrasion and impact, the carcass provides structural support, and the bottom cover reduces friction.
Customization:
- Conveyor belts can be customized by adjusting the materials and thickness of each component to meet specific operational requirements. This customization ensures that the belt can handle unique challenges in different mining environments.
Maintenance and Replacement:
- Understanding the role of each component helps in maintaining and replacing the conveyor belt. Regular inspections can identify wear and tear in specific components, allowing for timely repairs and replacements to avoid operational disruptions.
Types of Conveyor Belts and Their Maintenance Needs
Conveyor belts come in various types, each designed to meet specific operational requirements and environmental conditions in mining and other industries. Understanding the different types and their maintenance needs is essential for ensuring optimal performance, longevity, and cost-efficiency. Here, we will explore multi-ply, straight-warp, steel-cord, solid woven, heat-resistant, and nylon conveyor belt options.
Multi-ply Conveyor Belts
Definition: Multi-ply conveyor belts consist of multiple layers (or plies) of fabric that are bonded together to form a durable and strong belt. These layers typically include a combination of polyester and nylon fabrics.
Applications:
- Commonly used in general material handling, mining, and heavy-duty applications where high tensile strength and flexibility are required.
Maintenance Needs:
- Regular Inspections: Frequent checks for signs of wear, especially at the splice points and edges, which are prone to fraying and damage.
- Cleaning: Regular cleaning to remove debris and material buildup that can cause abrasion and reduce belt life.
- Tension Adjustment: Periodic tension adjustments to prevent slippage and ensure smooth operation.
- Splice Monitoring: Ensuring that splices are in good condition, as weak splices can lead to belt failure.
Straight-warp Conveyor Belts
Definition: Straight-warp conveyor belts feature a unique construction where the warp (longitudinal) and weft (transverse) fibers are not interwoven but are placed in a straight configuration. This design enhances strength and impact resistance.
Applications:
- Ideal for heavy-duty and high-impact applications such as mining, quarrying, and bulk material handling.
Maintenance Needs:
- Impact Damage Checks: Regular inspections for damage from heavy impacts, which can weaken the belt over time.
- Edge Protection: Ensuring edges are intact to prevent fraying and tearing.
- Surface Wear: Monitoring the belt surface for signs of wear and abrasion, particularly in high-load areas.
- Tension Control: Maintaining appropriate tension to avoid excessive wear and prolong belt life.
Steel-cord Conveyor Belts
Definition: Steel-cord conveyor belts are reinforced with steel cords, providing exceptional tensile strength and durability. These belts are designed to carry heavy loads over long distances.
Applications:
- Commonly used in mining, port facilities, and large-scale material transport operations where high strength and long-distance conveying are required.
Maintenance Needs:
- Regular Inspections: Routine checks for signs of rust or corrosion on the steel cords, which can compromise belt integrity.
- Non-destructive Testing: Using techniques such as X-ray or magnetic imaging to detect internal damage or cord breakage.
- Edge Care: Ensuring edges are protected from fraying and damage.
- Belt Alignment: Regularly checking and maintaining proper belt alignment to prevent uneven wear and potential belt failure.
Solid Woven Conveyor Belts
Definition: Solid woven conveyor belts are made from a single, solid woven fabric covered with a rubber coating. This construction provides high strength, flexibility, and resistance to tearing.
Applications:
- Suitable for underground mining, coal handling, and other applications where flame resistance and strength are critical.
Maintenance Needs:
- Flame Resistance Checks: Ensuring the flame-resistant properties are intact, especially after exposure to high temperatures.
- Surface Maintenance: Regular cleaning to remove buildup and prevent abrasion.
- Structural Integrity: Checking for any signs of tearing or weakening in the woven fabric.
- Belt Tension: Maintaining proper tension to ensure smooth operation and reduce wear.
Heat-resistant Conveyor Belts
Definition: Heat-resistant conveyor belts are designed to withstand high temperatures without degrading. They are typically made from heat-resistant materials such as special rubber compounds.
Applications:
- Used in industries where materials are transported at high temperatures, such as cement plants, steel mills, and foundries.
Maintenance Needs:
- Temperature Monitoring: Regularly monitoring the temperature exposure to ensure it remains within the belt’s specified range.
- Heat Damage Inspections: Checking for signs of heat damage, such as hardening, cracking, or blistering of the belt surface.
- Cleaning: Removing any material buildup that can act as an insulator and increase belt temperature.
- Belt Conditioning: Applying conditioners or treatments to maintain the belt’s flexibility and heat resistance properties.
Nylon Conveyor Belts
Definition: Nylon conveyor belts are constructed using nylon fibers, which provide excellent strength, flexibility, and resistance to wear and tear. These belts are designed to handle demanding applications where high tensile strength and durability are essential.
Applications:
- Commonly used in mining, material handling, and heavy-duty industrial applications.
- Ideal for operations requiring flexibility and strength, such as those involving sharp or abrasive materials.
Maintenance Needs:
- Regular Inspections:
- Conduct frequent checks for signs of wear and tear, particularly focusing on edges and splice points that are susceptible to damage.
- Cleaning:
- Perform regular cleaning to remove debris and material buildup that can cause abrasion and decrease the lifespan of the belt.
- Tension Adjustment:
- Periodically adjust the belt tension to prevent slippage and ensure smooth operation.
- Splice Monitoring:
- Regularly monitor the condition of splices, as weak or damaged splices can lead to belt failure. Ensure they are secure and intact to maintain the belt’s integrity.
Regular Maintenance Practices for Conveyor Belts
Regular maintenance is essential to ensure the optimal performance, safety, and longevity of conveyor belts, especially in demanding environments such as mining. This section will expand on inspection routines and common issues with their corresponding solutions.
Inspection Routines
1. Visual Inspection:
- Frequency: Daily or weekly.
- Purpose: Identify visible signs of wear and tear, damage, and misalignment.
- Components to Check:
- Belt Surface: Look for signs of abrasion, cuts, or punctures.
- Edges: Check for fraying or damage along the belt edges.
- Splices: Ensure that splices are secure and intact without separation.
- Rollers and Pulleys: Inspect for wear, alignment, and any debris that could cause jamming or damage.
- Idlers: Ensure they are rotating freely without excessive noise or vibration.
- Tools Needed: Flashlight, inspection mirror, and notepad for recording findings.
2. Detailed Mechanical Inspection:
- Frequency: Monthly or quarterly.
- Purpose: Perform a thorough check of the conveyor system’s mechanical components.
- Components to Check:
- Belt Tension: Ensure proper tension to avoid slippage and excessive wear.
- Alignment: Check for proper tracking and alignment to prevent belt drift.
- Bearings: Inspect bearings for lubrication and signs of wear or overheating.
- Drive Mechanism: Examine motors, reducers, and couplings for proper function and lubrication.
- Structural Integrity: Inspect the framework for signs of fatigue, cracks, or corrosion.
- Tools Needed: Wrenches, alignment tools, tension gauge, and lubrication equipment.
3. Non-destructive Testing:
- Frequency: Annually or as needed based on the belt’s condition.
- Purpose: Detect internal issues not visible during visual inspections.
- Techniques:
- Ultrasonic Testing: Identify internal defects or thickness variations.
- X-ray or Magnetic Imaging: Detect breaks or weaknesses in steel cords or hidden layers.
- Tools Needed: Ultrasonic testing equipment, X-ray machines, or magnetic imaging devices.
Common Issues and Solutions
1. Belt Misalignment:
- Issue: The belt deviates from its intended path, causing uneven wear and potential damage.
- Causes: Improper installation, uneven loading, or worn components.
- Solutions:
- Adjust Tracking: Use tracking devices or adjust pulleys and idlers to align the belt.
- Regular Inspections: Ensure consistent inspection and correction of alignment issues.
- Load Distribution: Ensure even loading across the belt to prevent skewing.
2. Slippage:
- Issue: The belt slips on the drive pulley, reducing efficiency and causing wear.
- Causes: Incorrect tension, worn pulleys, or improper belt-pulley contact.
- Solutions:
- Adjust Tension: Use a tension gauge to set the correct tension.
- Replace Worn Pulleys: Inspect and replace worn or damaged pulleys.
- Check Contact Surface: Ensure the belt and pulley surfaces are clean and free of debris.
3. Belt Wear and Tear:
- Issue: The belt surface or edges show signs of abrasion, cuts, or punctures.
- Causes: Abrasive materials, sharp objects, or improper handling.
- Solutions:
- Regular Cleaning: Remove debris and contaminants from the belt surface.
- Protective Covers: Use belt scrapers and covers to protect against abrasive materials.
- Repair Kits: Use repair kits for minor damage to extend belt life.
4. Splice Failure:
- Issue: Belt splices become weak or separated, causing interruptions and potential belt failure.
- Causes: Improper splicing techniques, excessive tension, or old age.
- Solutions:
- Proper Splicing: Ensure splices are done using the correct methods and materials.
- Regular Inspection: Frequently inspect splices for signs of wear or separation.
- Replace Old Splices: Replace splices that show significant wear or are nearing the end of their life expectancy.
5. Idler and Roller Issues:
- Issue: Idlers and rollers can become stuck, misaligned, or worn, causing increased friction and belt wear.
- Causes: Lack of lubrication, debris buildup, or mechanical wear.
- Solutions:
- Regular Lubrication: Ensure all moving parts are properly lubricated.
- Clean Rollers: Remove debris and check for smooth operation.
- Replace Worn Components: Inspect and replace any worn or damaged idlers and rollers.
6. Material Spillage:
- Issue: Material spills over the sides of the belt, causing wastage and potential blockages.
- Causes: Overloading, improper belt tension, or misalignment.
- Solutions:
- Proper Loading: Ensure materials are loaded evenly and within the belt’s capacity.
- Belt Skirting: Use skirting to prevent material from spilling over the sides.
- Regular Maintenance: Keep the belt and surrounding areas clean and free from obstructions.
Specific Maintenance for Different Mining Environments
Mining environments can vary significantly, and so do the maintenance strategies required to keep conveyor belts running efficiently. The primary difference lies between underground and surface mining operations, each presenting unique challenges and maintenance needs. This section will explore the specific maintenance strategies for these two distinct mining environments.
Underground Mining Maintenance Strategies
Challenges:
- Confined Spaces: Underground mines have limited space, making access and maneuverability challenging.
- Fire Hazards: The risk of fire is higher due to the enclosed environment and the presence of flammable materials.
- Moisture and Corrosion: High humidity and water ingress can lead to corrosion and degradation of materials.
- Dust and Debris: Dust accumulation can cause respiratory hazards and machinery wear.
Maintenance Strategies:
- Enhanced Fire Safety Measures:
- Flame-Resistant Belts: Use conveyor belts made from flame-resistant materials to minimize fire risks.
- Regular Fire Drills and Training: Conduct fire safety drills and train personnel on emergency response procedures.
- Fire Suppression Systems: Install and maintain fire suppression systems such as sprinklers and fire extinguishers.
- Corrosion Control:
- Coating and Sealing: Apply anti-corrosion coatings to metal components to protect against moisture.
- Waterproofing Measures: Ensure proper drainage and waterproofing to prevent water accumulation in the mine.
- Material Selection: Use corrosion-resistant materials for key components.
- Dust Management:
- Dust Suppression Systems: Implement dust suppression measures such as water sprays and dust collectors.
- Regular Cleaning: Perform frequent cleaning to remove dust and debris from conveyor belts and surrounding areas.
- Personal Protective Equipment (PPE): Provide PPE such as masks and respirators to workers.
- Accessibility Improvements:
- Modular Components: Use modular conveyor belt components that can be easily assembled and disassembled in confined spaces.
- Maintenance Platforms: Install maintenance platforms and access points to facilitate easier inspection and repair.
- Routine Inspections:
- Frequent Checks: Conduct daily or weekly inspections to identify and address issues promptly.
- Detailed Logging: Maintain detailed logs of maintenance activities and inspection findings for tracking and analysis.
Surface Mining Maintenance Strategies
Challenges:
- Exposure to Elements: Surface operations are exposed to weather conditions such as rain, heat, and UV radiation.
- Heavy Loads and Impact: Handling larger loads and dealing with the impact from heavy machinery and transported materials.
- Variable Terrains: Navigating diverse terrains that can cause wear and tear on conveyor belts.
Maintenance Strategies:
- Weather Protection:
- UV-Resistant Belts: Use belts with UV-resistant coatings to prevent degradation from sun exposure.
- Weather Shields: Install weather shields and covers to protect conveyor belts from rain and extreme weather.
- Temperature Monitoring: Monitor temperatures and take preventive measures to protect belts from thermal damage.
- Impact and Load Management:
- Reinforced Belts: Use reinforced conveyor belts that can withstand heavy loads and impact.
- Shock Absorbers: Install shock absorbers and impact beds to reduce the stress on belts and structures.
- Load Distribution: Ensure even distribution of load to prevent overloading and uneven wear.
- Terrain Adaptation:
- Flexible Belt Design: Use belts designed to navigate varying terrains, including inclines and declines.
- Regular Adjustment: Adjust and align belts regularly to accommodate changes in terrain and prevent misalignment.
- Terrain-Specific Solutions: Implement specific solutions such as sidewall belts for steep inclines or mobile conveyors for shifting terrains.
- Preventive Maintenance:
- Scheduled Maintenance: Develop and adhere to a preventive maintenance schedule to address potential issues before they escalate.
- Lubrication: Ensure regular lubrication of moving parts to reduce friction and wear.
- Component Replacement: Replace worn or damaged components promptly to avoid operational disruptions.
- Safety Measures:
- Barrier Systems: Install barriers and safety guards to protect workers from moving parts.
- Emergency Stops: Ensure that emergency stop mechanisms are in place and easily accessible.
- Training: Provide ongoing training for workers on safe operating procedures and emergency response.
Fireproofing and Safety Checks
Fireproofing and safety checks are critical components of maintaining conveyor belts in mining operations, especially in environments where fire hazards are significant. Compliance with safety standards, such as the Mine Safety and Health Administration (MSHA) Part 14 requirements, is essential to ensure the safety of workers and equipment. This section will expand on MSHA Part 14 requirements and best practices for fireproofing and conducting safety checks.
MSHA Part 14 Requirements
The Mine Safety and Health Administration (MSHA) Part 14 regulations set forth stringent requirements for the approval of conveyor belts used in underground coal mines. These regulations aim to reduce the risk of fire and ensure that conveyor belts can withstand the harsh conditions of mining operations.
Key Requirements:
- Flame Resistance:
- Conveyor belts must be made from materials that are resistant to ignition and capable of self-extinguishing. This is to prevent the spread of fire along the belt surface.
- Testing and Certification:
- Conveyor belts must undergo rigorous testing to ensure compliance with flame resistance standards. This includes laboratory tests that simulate fire conditions to evaluate the belt’s performance.
- Only belts that pass these tests receive MSHA Part 14 certification, indicating they meet the necessary safety standards.
- Identification and Labeling:
- Certified conveyor belts must be clearly marked with the MSHA approval number and flame resistance rating. This labeling helps in the identification and ensures that only compliant belts are used in mining operations.
- Documentation and Recordkeeping:
- Manufacturers must provide detailed documentation, including test reports and certification records, to demonstrate compliance with MSHA Part 14 requirements.
- Mining operators are required to maintain records of all conveyor belts in use, including their certification status and maintenance history.
Best Practices for Fireproofing
1. Use of Flame-Resistant Materials:
- Material Selection: Choose conveyor belts made from flame-resistant materials that meet or exceed MSHA Part 14 requirements.
- Regular Upgrades: Periodically review and upgrade conveyor belts to ensure they incorporate the latest advancements in flame-resistant technology.
2. Installation of Fire Suppression Systems:
- Automatic Sprinklers: Install automatic sprinkler systems along the conveyor belt route to quickly extinguish any fires that may start.
- Fire Extinguishers: Place fire extinguishers at strategic locations for easy access by personnel in case of an emergency.
- Fire Detection Systems: Implement advanced fire detection systems, such as thermal sensors and smoke detectors, to provide early warning and enable rapid response.
3. Firebreaks and Barriers:
- Physical Barriers: Use fire-resistant barriers and enclosures to isolate conveyor belts from other critical areas of the mine.
- Firebreaks: Create firebreaks by removing combustible materials and installing non-combustible barriers around the conveyor belt system.
4. Proper Ventilation:
- Ventilation Systems: Ensure adequate ventilation to disperse heat and smoke, reducing the risk of fire spread.
- Regular Maintenance: Maintain and clean ventilation systems to ensure they function effectively and prevent the buildup of flammable gases and dust.
Best Practices for Safety Checks
1. Regular Inspections:
- Daily Visual Checks: Conduct daily visual inspections to identify any signs of wear, damage, or potential fire hazards on the conveyor belt and surrounding areas.
- Detailed Monthly Inspections: Perform detailed inspections at least once a month, focusing on the condition of the belt, splices, rollers, and fire suppression systems.
2. Maintenance of Fire Suppression Systems:
- Routine Testing: Regularly test fire suppression systems to ensure they are in working order and can respond effectively in an emergency.
- System Upgrades: Upgrade fire suppression systems periodically to incorporate the latest technology and improve their effectiveness.
3. Training and Drills:
- Employee Training: Provide comprehensive training to all employees on fire safety protocols, the use of fire suppression equipment, and emergency response procedures.
- Regular Drills: Conduct regular fire drills to ensure that all personnel are familiar with evacuation routes and emergency procedures.
4. Recordkeeping and Documentation:
- Maintenance Logs: Maintain detailed logs of all maintenance activities, inspections, and safety checks. This documentation helps track the condition of the conveyor belt and compliance with safety standards.
- Incident Reports: Record any fire incidents or near-misses, including the cause, response actions, and lessons learned. Use this information to improve fire safety practices.
5. Collaboration with Authorities:
- Regular Audits: Collaborate with MSHA and other regulatory authorities for regular audits and inspections to ensure ongoing compliance with safety standards.
- Feedback and Improvement: Use feedback from regulatory audits and inspections to continually improve fireproofing and safety practices.
Durability Factors for Conveyor Belts
Durability is a critical aspect of conveyor belt performance, especially in demanding environments such as mining. Various factors influence the durability of conveyor belts, including pulley diameter, corrosion resistance, and the nature of materials used in their construction. Understanding and optimizing these factors can significantly enhance the lifespan and reliability of conveyor belts.
Pulley Diameter
Definition: Pulley diameter refers to the size of the pulleys that support and drive the conveyor belt. It is a crucial factor that affects the belt’s bending stress and overall durability.
Importance:
- Bending Stress: Larger pulley diameters reduce the bending stress on the conveyor belt as it wraps around the pulley. This minimizes the risk of fatigue and cracking, especially in belts with stiff reinforcement layers such as steel cords.
- Belt Flexibility: Belts with higher flexibility can accommodate smaller pulley diameters, but frequent flexing over small diameters can still lead to premature wear and tear.
- Tension Distribution: Proper pulley diameter ensures even distribution of tension across the belt, preventing localized stress that can cause damage.
Best Practices:
- Selecting Appropriate Diameter: Choose pulley diameters that are compatible with the belt’s construction and the operational requirements. Follow manufacturer guidelines to ensure the diameter is sufficient to minimize bending stress.
- Regular Inspection: Inspect pulleys regularly for wear and alignment issues. Ensure that pulleys are free from debris and properly lubricated to reduce friction and wear on the belt.
- Maintenance: Replace worn or damaged pulleys promptly to prevent additional stress and damage to the conveyor belt.
Corrosion Resistance
Definition: Corrosion resistance refers to the ability of the conveyor belt and its components to withstand degradation caused by chemical reactions with environmental elements such as moisture, chemicals, and acids.
Importance:
- Environmental Exposure: Conveyor belts, especially those used in mining, are often exposed to harsh conditions that can include moisture, acidic or alkaline substances, and other corrosive agents.
- Longevity: High corrosion resistance extends the life of the belt by preventing deterioration of the materials used in its construction, such as the carcass and the covers.
- Maintenance Costs: Corrosion-resistant materials reduce the frequency and cost of maintenance and replacements, contributing to overall operational efficiency and cost-effectiveness.
Best Practices:
- Material Selection: Use materials with inherent corrosion resistance, such as stainless steel for reinforcement cords and high-quality rubber compounds for covers. In some cases, synthetic materials like PVC and polyurethane are also effective.
- Protective Coatings: Apply anti-corrosion coatings to metal components, including pulleys, idlers, and framework, to enhance their resistance to environmental factors.
- Environmental Control: Implement measures to control environmental exposure, such as proper ventilation to reduce humidity, and protective barriers to shield the conveyor system from chemical splashes or spills.Material Nature
Definition: The nature of materials used in the construction of conveyor belts includes the type of polymers, reinforcement fibers, and any additional coatings or treatments applied to enhance performance.
Importance:
- Abrasion Resistance: The material composition of the belt impacts its ability to resist wear and tear from abrasive materials being transported, such as coal, ores, and rocks.
- Temperature Resistance: Different materials have varying degrees of resistance to high or low temperatures, which can affect their performance and durability in specific applications.
- Flexibility and Strength: The balance between flexibility and tensile strength is crucial for accommodating different operational demands, such as heavy loads and varying terrains.
Best Practices:
- Material Selection: Choose materials that are specifically designed to handle the operational conditions of the mining environment. For example:
- Rubber Compounds: High-quality rubber compounds provide excellent abrasion and impact resistance.
- Synthetic Polymers: Materials like PVC and polyurethane offer good flexibility, chemical resistance, and suitability for specific environments.
- Reinforcement Fibers: Use steel cords or synthetic fibers (e.g., polyester, nylon) to enhance tensile strength and reduce elongation under load.
- Custom Coatings: Apply custom coatings to address specific needs, such as heat-resistant or oil-resistant coatings, to protect the belt from high temperatures or chemical exposure.
- Regular Testing: Perform regular testing of belt materials to assess their condition and performance under operational stresses. This includes checking for signs of degradation, such as cracking, hardening, or loss of flexibility.
SEE ALSO: The Ultimate Guide to Knowledge Management: Exploring Intranets and Wikis
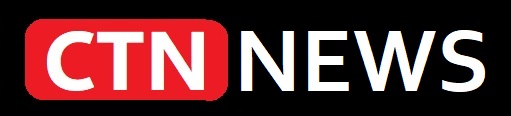
Learning
First-Time Buyer’s Guide to the UK Property Market
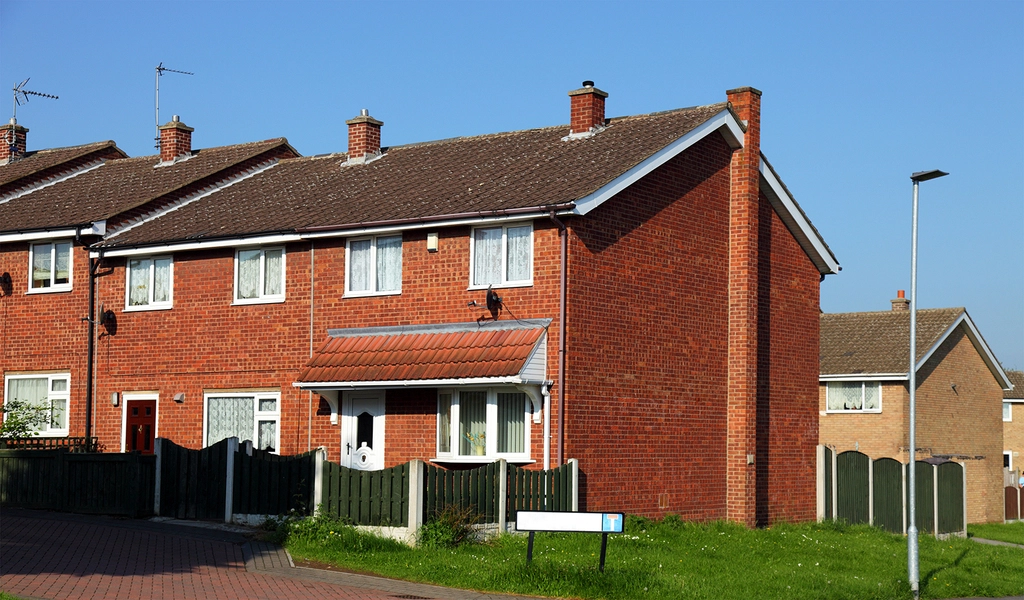
Entering the UK property market as a first-time buyer can feel both exciting and daunting. The process is filled with potential pitfalls and complex decisions, but with the right guidance, it can be navigated smoothly. The estate agents in Yorkshire demystify the journey from the initial decision to buy a home to the moment you step over the threshold of your new property.
Understanding Your Financial Position
The first and perhaps most crucial step in the home-buying process is understanding your financial situation. This includes assessing your savings, income, and current debts. Here’s how you can prepare:
1. Deposit: Generally, you’ll need at least 5% of the property price as a deposit, though aiming for 10% or more can provide better mortgage rates.
2. Income and Expenses: Use a budget planner to assess your monthly income against your expenses. This will help you understand how much you can afford in monthly mortgage repayments.
3. Credit Score: Lenders will evaluate your credit score to determine your mortgage eligibility. So it’s important to have a good credit score, and you should work on it if required.
4. Mortgage Options: Speak to a mortgage advisor to understand different types of mortgages, such as fixed-rate, variable-rate, and help-to-buy schemes.
Getting a Mortgage Agreement in Principle
A Mortgage Agreement in Principle (AIP) is a statement from a lender indicating how much they’ll likely lend you. You will be a more attractive buyer with an AIP as it shows sellers you’re serious and financially prepared.
Deciding What You Want
Before you start viewing properties, it’s essential to know what you’re looking for. Consider the following factors:
1. Location: Proximity to work, schools, public transport, and amenities are key. Research neighbourhoods to find the best fit for your lifestyle.
2. Property Type: Decide whether you want a flat, terraced house, semi-detached, or detached property. Each has its pros and cons.
3. Must-Haves: Make a list of non-negotiables, such as the number of bedrooms, garden size, and parking facilities.
4. Future Proofing: Consider your future needs. Are you planning to start a family? Do you need space for a home office?
Starting the Property Search
With a clear idea of what you’re looking for, you can begin your property search. Here are some tips:
1. Use Online Portals: Websites like Rightmove, Zoopla, and OnTheMarket are excellent starting points. Set up alerts to get notified of new listings that meet your criteria.
2. Visit Estate Agents: Register with local estate agents who can provide insights into the market and inform you of new properties before they’re listed online.
3. Attend Viewings: Don’t rush this part. Visit several properties to get a feel for what’s available in your price range.
Making an Offer
Once you find a property you love, it’s time to make an offer. Here’s how to approach it:
1. Research: Check the selling prices of similar properties in the area to gauge a fair offer.
2. Negotiate: Don’t be afraid to negotiate. The starting point is most usually the asking price.
3. Conditions: You might include conditions in your offer, such as the inclusion of certain fixtures or a specific moving date.
The Legal Process
If your offer is accepted, the legal process begins. You’ll need a solicitor or licensed conveyancer to handle the legalities. Here’s what to expect:
1. Conveyancing: This is the legal transfer of property ownership. Your solicitor will handle this, including conducting searches, dealing with the Land Registry, and transferring the funds.
2. Surveys and Inspections: Arrange for a property survey to check for structural issues. There are different types of surveys, from basic condition reports to full structural surveys.
3. Mortgage Finalisation: Once the survey is complete and satisfactory, your mortgage can be finalised.
4. Exchange of Contracts: This is when the sale becomes legally binding. You’ll pay your deposit at this stage.
5. Completion: On the agreed completion date, the remaining money is transferred, and you receive the keys to your new home.
Moving In
Moving day can be hectic, but planning can ease the stress:
1. Hire a Removal Company: Book a reliable removal company well in advance. Discover the best deals by getting quotes from multiple companies.
2. Pack Strategically: Label your boxes by room and keep essential items accessible.
3. Notify Utilities and Change Address: Inform your utility providers of your move date and update your address with banks, the DVLA, and other important institutions.
Settling In
Get settled. Introduce yourself to the neighbours, familiarise yourself with the local area, and really start to make the place your own.
Here are a few final tips:
1. Safety Checks: Make sure that your smoke alarms and carbon monoxide detectors are working, and make sure that you know where the gas and electricity meters are located.
2. Maintenance Plan: Keep a record of the smooth functioning of your new home with a maintenance schedule, complete with regular checks and seasonal tasks.
3. Personal Touches: Add personal touches to make the space feel like home. This can be from putting up family photos or redoing the decoration in your rooms.
Conclusion
Buying your very first home in the UK is most definitely a milestone, difficult and full of challenges but rewarding in the end. Such a philosophy guides you in understanding finances and knowing what you want to achieve from detailed research, and seeking professional advice that confidently helps you navigate the property market. Yes, the journey may have its hurdles, but in the end—owning your own home—the reward will be worth the effort. Welcome to your new chapter!
SEE ALSO: Conquer the Chaos: Hacks to Clean Your Home in Half the Time
Learning
5 Health Benefits of Regular Pedicures
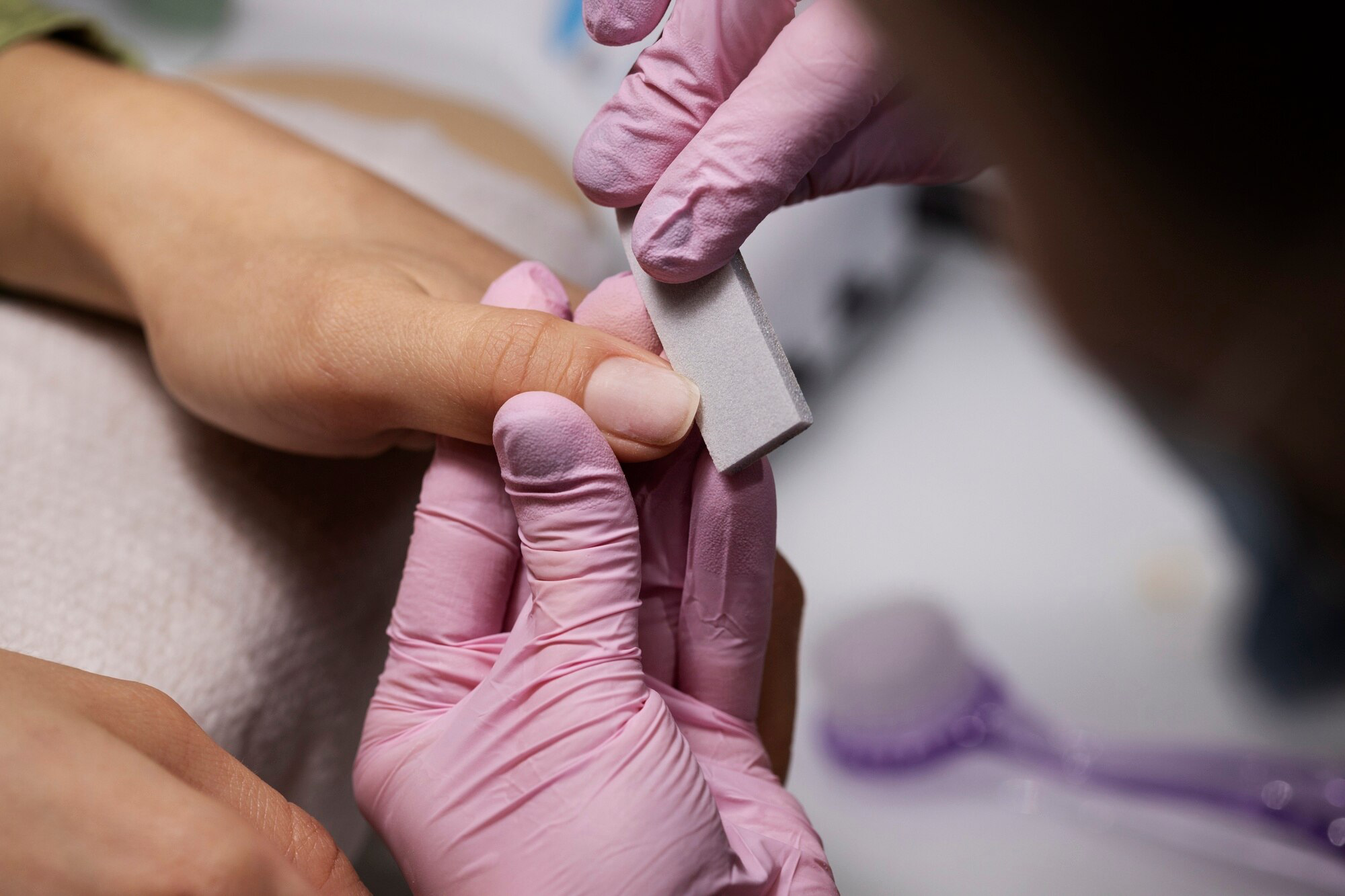
There’s nothing quite like a pedicure to keep your feet looking and feeling their best, but did you know that pedicures do more than simply enhance the appearance of your feet? Many people don’t realize that regular pedicures can come with a wide range of health benefits that can promote the well-being of your feet, so here are some ways that your routine pedicure keeps both your toenails and feet in the best condition possible!
Smoother Skin
One of the biggest misconceptions about pedicures is that they only cater to and look after your toenails. While you’ll definitely be leaving each session with a fresh coat of nail polish, your pedicure can also do wonders for the health of your skin. Aside from trimming and shaping your nails and cuticles, you’ll notice that your nail technician also dedicates a few steps to the skin of your feet.
After inspecting your feet and looking for any issues or imperfections that may need to be addressed, your technician will work on an exfoliating scrub to remove any dead skin cells. This step may also be aided by a foot file, which can be used to buff away any calluses and other problem areas manually.
Softer Skin
After your nail technician addresses all the problem areas of your feet and removes any unwanted dead skin cells, he or she will often massage in a moisturizing product, such as lotion, cream, or butter, to ensure that your skin is properly moisturized. These products contain skin-loving ingredients that will ensure that your feet have everything they need to look and feel their best so that you can walk out of your pedicure with a renewed sense of confidence.
Healthier Nails
After your pedicure session, your nails will not only look better due to the fresh coat of nail polish, but they’ll also be healthier and stronger. This is because your nail technician takes their time to ensure that your nails are properly looked after through steps that include deep cleaning, nail trimming, nail filing, and cuticle care. All of these things work together to prevent issues like ingrown nails from occurring, all the while improving the appearance of your nails.
Increased Blood Circulation
While the specific steps included in your pedicure will depend on the beauty salon, most pedicures will have a massage step somewhere in the mix. One of the often overlooked benefits of these massages is the increased blood circulation, which can deliver more nutrients and oxygen to your feet and nails, promoting their health and appearance. Aside from that, better blood flow means reduced tension and soreness, as well as better distributed heat throughout your body.
Reduced Infections
A significant amount of dirt and bacteria can build up on your feet without you even realizing it, but pedicures can be a great way to prevent these from happening in the first place. The exfoliation step of a pedicure removes dead skin cells as well as all the debris that may have accumulated underneath, and the deep cleaning of your toenails and cuticles also gets rid of any impurities that may have slipped beneath them, which can stop infections from happening.
These are some of the many health benefits that you can look forward to at your next pedicure appointment. However, it’s worth noting that you need to book regular sessions to truly reap all the rewards. This can be difficult, especially when you don’t feel like driving to your nearest nail salon after a long day, but the good news is that you can enjoy the salon experience in the comfort of your own home with a home pedicure service.
Learning
Commercial Boiler Installation Services London
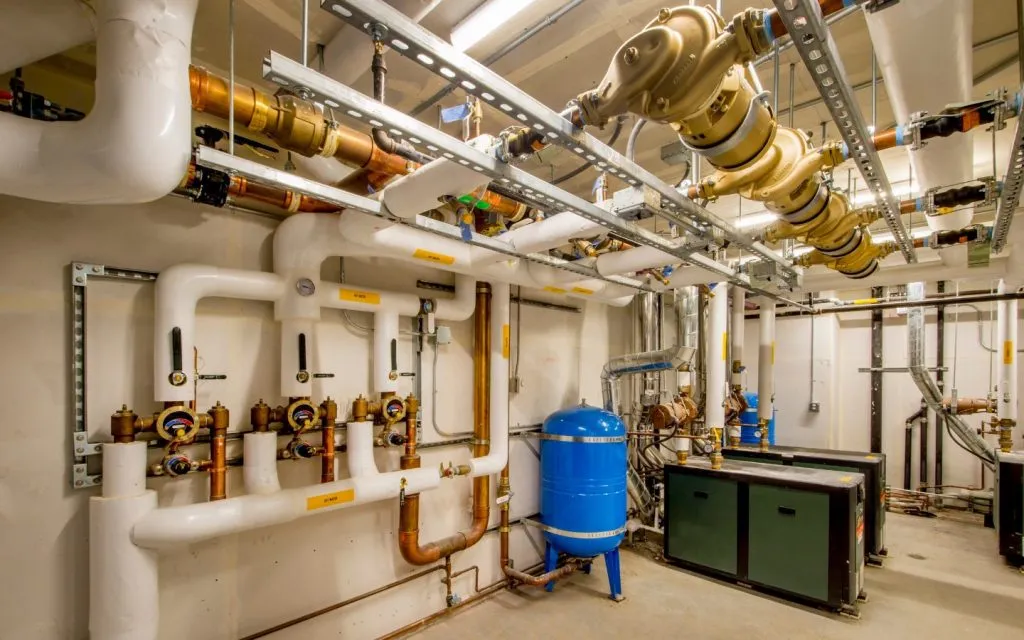
For businesses in the bustling city of London, having a reliable heating system is crucial. Whether you’re opening a new office, expanding your current premises, or simply upgrading an outdated system, commercial boiler installation services for businesses in London are essential to ensure your operations run smoothly and efficiently. Proper installation and maintenance of commercial boilers can make a significant difference in energy efficiency, cost savings, and the overall comfort of your workspace.
The Importance of Professional Installation
When it comes to installing a commercial boiler, professional expertise is paramount. Here’s why:
- Efficiency and Performance: Professional installation ensures that your boiler operates at peak efficiency, reducing energy consumption and lowering utility bills. A well-installed boiler can effectively meet the heating demands of your business without unnecessary energy waste.
- Safety: Commercial boilers are complex systems that require precise installation to operate safely. Professional installers adhere to stringent safety standards and regulations, minimizing the risk of accidents and ensuring the safety of your employees and premises.
- Compliance with Regulations: Commercial properties are subject to various building codes and regulations. Professional installers are well-versed in these requirements and ensure that your boiler system complies with all local laws and standards.
- Longevity and Reliability: Proper installation is critical to the longevity and reliability of your boiler. A professional installation can prevent common issues such as leaks, pressure problems, and system failures, ensuring that your boiler runs smoothly for years to come.
Key Considerations for Commercial Boiler Installation
When planning for a commercial boiler installation, several factors need to be considered:
- Type of Boiler: The type of boiler you choose will depend on your business’s specific needs. Options include gas boilers, oil boilers, and electric boilers, each with its own set of advantages. Consulting with a professional can help you determine the best choice for your business.
- Sizing and Capacity: The boiler’s size and capacity must match the heating demands of your commercial space. An undersized boiler will struggle to meet your needs, while an oversized one will lead to inefficiencies and higher costs.
- Location: The placement of your boiler affects its efficiency and accessibility for maintenance. Professional installers can help you choose the optimal location for your boiler.
- Integration with Existing Systems: If you’re upgrading or replacing an existing boiler, it’s essential to ensure compatibility with your current heating system. Professional installers can seamlessly integrate the new boiler with your existing setup.
Choosing the Right Installation Service
Selecting the right installation service provider is crucial to the success of your boiler installation project. Consider the following when making your choice:
- Experience and Expertise: Look for a provider with a proven track record in commercial boiler installations. Experienced installers can handle the complexities of commercial systems and provide high-quality workmanship.
- Reputation: Check reviews and testimonials from previous clients to gauge the provider’s reliability and customer satisfaction.
- Comprehensive Services: Choose a provider that offers a full range of services, including installation, maintenance, and repair. This ensures that all your boiler needs are met by a single, trusted source.
In London, ROWLEN is a reputable name known for delivering top-notch commercial boiler installation services. Their team of experts is dedicated to providing efficient, safe, and compliant installations tailored to the unique needs of businesses.
Conclusion
Investing in professional commercial boiler installation services for businesses in London is essential for ensuring efficiency, safety, and long-term reliability. By choosing an experienced and reputable service provider like ROWLEN, you can rest assured that your heating system will be installed correctly and maintained to the highest standards. Proper installation not only enhances the performance of your boiler but also contributes to the overall comfort and productivity of your business environment.
SEE ALSO:
-
News4 years ago
Let’s Know About Ultra High Net Worth Individual
-
Entertainment2 years ago
Mabelle Prior: The Voice of Hope, Resilience, and Diversity Inspiring Generations
-
Health4 years ago
How Much Ivermectin Should You Take?
-
Tech2 years ago
Top Forex Brokers of 2023: Reviews and Analysis for Successful Trading
-
Lifestyles3 years ago
Aries Soulmate Signs
-
Movies3 years ago
What Should I Do If Disney Plus Keeps Logging Me Out of TV?
-
Health3 years ago
Can I Buy Ivermectin Without A Prescription in the USA?
-
Learning3 years ago
Virtual Numbers: What Are They For?