Automotive
Fortune Cross Automotive Precision Shaft Factory in Thailand Demands Quality Control
In the highly competitive automotive industry, precision and quality are paramount. Automotive precision shafts, which are integral components in vehicles, must be manufactured with utmost accuracy. Fortune Cross Thailand, a reputed precision shaft manufacturer, exemplifies the importance of inspection and testing in quality control. This article explores the critical role these processes play in ensuring top-notch automotive precision shaft factory in Thailand.
Automotive precision shafts are mechanical components meticulously engineered to transmit torque and rotation. They are indispensable for the seamless functioning of various systems in vehicles, such as transmission, steering, and engine components. Precision shaft factory in Thailand plays a significant role in producing these vital components.
With quality control being the linchpin for ensuring safety, performance, and durability in the automotive sector, even a slight deviation in quality can have far-reaching consequences. Thus, precision shaft manufacturers in Thailand are committed to maintaining high standards in production and quality control.
Overview of Automotive Precision Shafts
Precision shafts are pivotal elements in the automotive industry, and their production involves intricate precision shaft machining processes. At Fortune Cross Thailand, the range of shafts produced is extensive and made from high-grade materials to ensure optimum performance. In this section, we delve into the role of precision shafts in the automotive industry, the various types produced by Fortune Cross Thailand, and the materials employed in manufacturing these shafts.
Role of Precision Shafts in the Automotive Industry:
- Power Transmission
Precision shafts are essential for transmitting power from the engine to other components, ensuring the vehicle operates efficiently.
- Structural Support
They provide crucial support within mechanical systems, helping to maintain structural integrity during operation.
- Reducing Friction and Wear
The high precision in their machining ensures minimal friction between moving parts, which reduces wear and tear and prolongs the lifespan of components.
Types of Precision Shafts available in Thailand:
- Shaft Lifter Arm (12×128.9 mm)
This is used in the valve train of engines to help control valve movement, ensuring proper timing and performance.
- Carburetor Shaft (6.0×67.6 mm)
A vital part of the carburetor in motorcycles, this shaft plays a crucial role in mixing air and fuel in the right proportion for combustion.
- Shaft Gear Shift (12.0×280.5 mm)
Integral to the transmission system, this shaft is responsible for helping the vehicle switch between gears smoothly and efficiently.
Materials Used for Manufacturing Precision Shafts:
- Japanese Steel (S45C)
A high-quality carbon steel, S45C is used for its strength and durability, making it suitable for components that undergo a lot of stress.
- SUS420J2 Stainless Steel
Known for its resistance to corrosion and high hardness, this steel is often used in applications where both durability and a high-quality finish are necessary.
- Additional Materials
Fortune Cross also utilizes other high-grade materials such as SUS420F, SUS303, and more, tailoring material choices to specific application requirements.
With precision shaft machining at the forefront, Fortune Cross Thailand’s dedication to producing high-quality precision shafts is evident in the materials they choose and the diverse range of products they manufacture. These shafts play a vital role in the automotive industry, and their quality and precision are paramount.
Importance of Inspection in Quality Control
Precision shafting is a process that requires meticulous attention to detail. Inspection plays a pivotal role in quality control for precision shafting, ensuring that the shafts meet the required specifications and performance criteria. Here, we will delve into the three main aspects of inspection that are fundamental in quality control: ensuring dimensional accuracy, material quality inspection, and surface finish inspection.
Ensuring Dimensional Accuracy:
- Diameter Control:
- Critical Role: An accurate diameter is crucial for the proper fitting of the shaft in the assembly.
- Operational Reliability: Ensures that the precision shaft can operate without excessive vibration or misalignment.
- Length Size Control:
- Compatibility: Controlling the length is vital for ensuring that the shaft fits seamlessly with other components.
- Structural Integrity: Accurate length helps in maintaining structural integrity and preventing over-stressing of components.
Material Quality Inspection:
- Ensuring the Use of High-Quality Materials:
- Durability: High-quality materials prolong the lifespan of the precision shaft, making it more resistant to wear and tear.
- Performance: Better materials contribute to the optimal performance of the shaft, as they can handle greater stresses and loads.
- Detecting Material Defects:
- Preventive Measure: Identifying material flaws early helps in preventing catastrophic failure in application.
- Cost-Effective: It is more economical to detect and address material defects at the manufacturing stage than dealing with breakdowns later on.
Surface Finish Inspection:
- Importance of Surface Finish:
- Friction Reduction: A smooth surface finish is vital in reducing friction, which in turn lowers the wear rate.
- Heat Dissipation: Improved surface finish enhances heat dissipation, which is crucial for the performance of the shaft.
- How It Affects Performance:
- Efficiency: A proper surface finish ensures that there is minimal energy loss due to friction, leading to higher operational efficiency.
- Maintenance: Well-finished surfaces require less maintenance and are less likely to cause premature failure of surrounding components.
Testing Procedures in Quality Control
Quality control is a linchpin in the manufacturing of automotive precision shafts. To ensure that these shafts meet the highest standards of durability, strength, and performance, a variety of testing procedures are employed. Here, we take a closer look at the different types of testing that are integral to maintaining the excellence of precision shafts manufactured by Fortune Cross Thailand.
Mechanical Testing:
Mechanical testing is instrumental in evaluating how materials behave under different conditions, ensuring that the shafts can endure the physical demands during use.
- Stress Tests
Stress tests are conducted to gauge how materials respond to different levels of stress. By applying force to the material and measuring its deformation and strength, stress tests are critical in understanding if the material is suitable for withstanding the operational demands.
- Fatigue Tests
Fatigue tests are essential for assessing the endurance of materials under cyclic or repeated loads. By subjecting the material to repeated loading and unloading, these tests simulate real-world conditions and are crucial for predicting lifespan and preventing premature failure.
Non-Destructive Testing (NDT):
NDT is vital for evaluating the integrity of materials and finished products without causing any damage, making it perfect for detecting internal defects that might not be externally visible.
- X-ray Testing
X-ray testing is utilized for detecting internal flaws and irregularities in materials. By using X-rays to inspect the internal structure and observing variations in absorption levels, internal flaws become discernible in the X-ray images.
- Ultrasonic Testing
Ultrasonic testing is an invaluable technique for inspecting the internal structure and integrity of materials. It uses high-frequency sound waves that traverse through the material, and the analysis of echo patterns is employed to identify any discontinuities or defects inside.
Performance Testing:
Performance testing ensures that the shafts are fully equipped to function effectively under conditions akin to real-world applications.
- Load Testing
Load testing verifies the shaft’s ability to endure specific loads during operation. This testing process involves applying forces that simulate the loads experienced in service to validate that the shaft will function as intended under these conditions.
- Operational Testing
Operational testing is employed to ensure that the shaft performs optimally in realistic environments. By simulating real-world operating conditions, this testing procedure evaluates the performance, efficiency, and reliability of the shaft.
Compliance with International Standards:
Ensuring compliance with international standards is crucial for products to meet globally recognized quality benchmarks.
- Adherence to Japanese Standards
Fortune Cross Thailand’s adherence to Japanese standards signifies a commitment to high-quality manufacturing processes. Japanese standards are globally renowned for their rigor in quality control, and adherence to them ensures the production of superior precision shafts.
- Certifications and Accreditations
Having certifications and accreditations ensures international recognition for the quality of products. It signifies that the products have undergone an independent assessment and satisfy international quality standards.
A Leading Precision Shaft Factory in Thailand
In the landscape of precision shaft manufacturing, there is a particular factory in Thailand that has set the bar high. This case study aims to shed light on the effective quality control processes, real-world applications, and customer feedback associated with this factory without explicitly mentioning its name.
Quality Control Processes Employed by Reliable Factories:
- Stringent Material Inspection
The factory ensures the materials used are of the highest quality, often utilizing high-grade steel such as S45C and SUS420J2, which are critical for the durability and performance of the precision shafts.
- Dimensional Accuracy Checks
Advanced measuring instruments are deployed to confirm the shaft dimensions are within prescribed tolerances, ensuring compatibility and efficient operation.
- Surface Finish Evaluation
The factory employs surface roughness testers to ensure that the surface finish of its products meets the required standards, thereby reducing friction and increasing the lifespan of the shafts.
- Regular Equipment Calibration
By calibrating its manufacturing equipment routinely, the factory guarantees consistent production quality.
- Adherence to International Standards
The factory complies with Japanese standards and other international benchmarks to ensure the quality and performance of its products.
Real-World Examples of Inspection and Testing for Precision Shafts:
- Customized Production for Clients
This factory has been noted for manufacturing customized precision shafts that meet specific client requirements. This involves special inspection and testing procedures to ensure client satisfaction.
- Swift Rectification of Defects
In instances where minor deviations or defects have been detected, the factory is known for acting promptly and effectively to maintain product integrity.
- Consistent High-Quality Output
Through the successful implementation of quality control processes, the factory has consistently delivered high-quality precision shafts to the market.
Customer Feedback and Reputation for Quality:
- High Customer Satisfaction
The factory has received positive feedback from customers regarding the quality and durability of their precision shafts.
- Recommendations and Referrals
A considerable number of new customers are derived through referrals, which suggests a high level of satisfaction among existing clients.
- Strong Market Presence
A steadfast commitment to quality has enabled this factory to establish a substantial market presence and become one of the preferred manufacturers of precision shafts.
In conclusion, this leading precision shaft factory in Thailand exemplifies the importance of rigorous quality control processes. Its strong market presence and positive customer feedback attest to the high standards maintained in the manufacturing of precision shafts.
The Future of Quality Control in Precision Shaft Manufacturing
As the automotive industry evolves, precision shaft manufacturers are confronted with new challenges and opportunities. Advancements in technology, shifts in industry trends, and the growing importance of sustainability are shaping the future of quality control in precision shaft manufacturing. This section delves into these key aspects, providing insights into what lies ahead for manufacturers in this domain.
- Technological Advancements in Inspection and Testing
- Artificial Intelligence (AI) and Machine Learning
AI algorithms and machine learning models are being integrated into inspection systems to predict and detect defects with greater accuracy. These technologies help in reducing human error and improving overall quality.
- 3D Scanning and Imaging
Modern 3D scanning and imaging techniques allow for highly detailed inspection of shaft dimensions and surface topology. This facilitates quicker and more accurate detection of deviations from specified tolerances.
- Robotic Process Automation (RPA)
Automating repetitive inspection tasks with robots not only increases efficiency but also ensures consistency in quality. RPA is particularly useful in high-volume production environments.
- Internet of Things (IoT)
IoT devices and sensors can monitor the manufacturing process in real time, enabling immediate feedback and adjustment. This leads to improved quality control and reduced waste.
- Industry Trends
- Customization and Personalization
As consumer demands diversify, there is a growing trend toward customization and personalization. Precision shaft manufacturers are adapting by offering more varied and tailored products without compromising quality.
- Integration of Big Data Analytics
Harnessing big data analytics allows manufacturers to gain insights from large datasets. This can be crucial for identifying patterns, trends, and potential areas of improvement in quality control processes.
- Globalization and Supply Chain Optimization
Precision shaft manufacturers are expanding their reach and optimizing supply chains to meet global demands. This requires stringent quality control to adhere to varying international standards.
- Sustainability and Environmental Considerations
- Use of Recycled Materials
The integration of recycled materials into manufacturing processes reflects a growing commitment to sustainability. This helps in reducing environmental impact and often comes with cost benefits.
- Energy-Efficient Manufacturing Processes
Implementing energy-efficient technologies and practices reduces the carbon footprint of manufacturing. This is not only environmentally responsible but can also be a selling point, especially for eco-conscious consumers.
- Sustainable Waste Management
Adopting sustainable waste management practices, such as recycling and repurposing waste material, minimizes environmental pollution and contributes to a circular economy.
Final Thoughts: Embracing Excellence in Automotive Precision Shafts Through Quality Control
Quality control, through meticulous inspection and testing, is indispensable in the production of automotive precision shafts. Fortune Cross Thailand exemplifies the implementation of these principles, producing exceptional products that cater to the automotive industry. Stakeholders must embrace rigorous quality control methods to ensure safety, performance, and durability.
Engage with the future of automotive precision manufacturing by investing in quality. Choose Fortune Cross Thailand for excellence in precision shafts.
Automotive
Russell’s early departure leaves Lando Norris on pole at the Hungarian F1 GP.
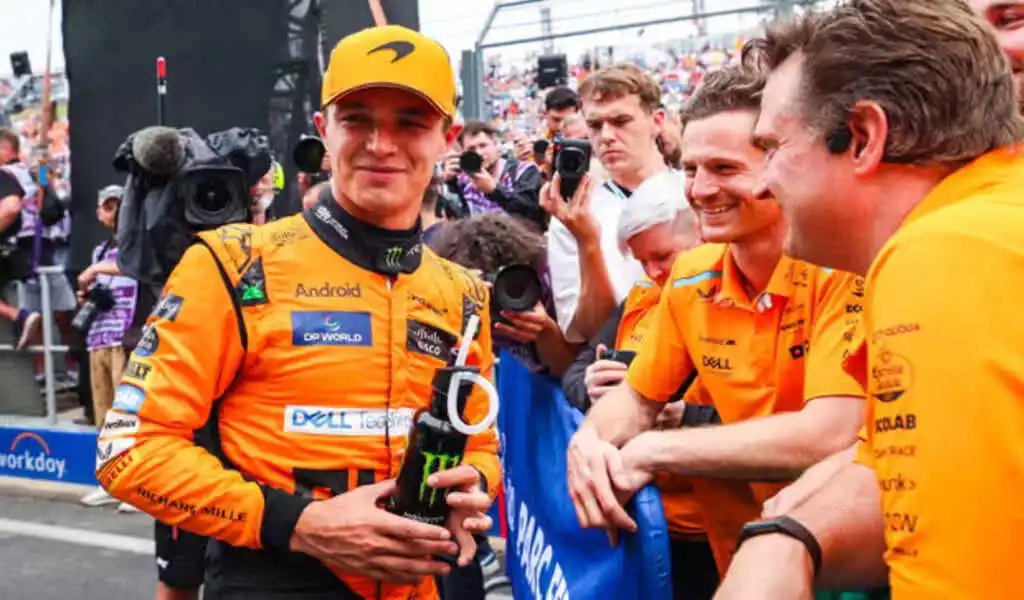
(CTN News) – Lando Norris and his McLaren squad survived a tough qualifying session for the Hungarian Grand Prix, but they know they must perform on Sunday.
Lando Norris needed to win Budapest after Oscar Piastri locked off the top row in the field’s fastest McLaren. Recent races have been costly owing to wasted opportunities and little mistakes.
He matched Max Verstappen’s pole lap at the Hungaroring, who was unhappy to finish third. In a confident and aggressive approach, the 24-year-old finished more than three tenths ahead of the Dutchman, hitting the apexes.
Piastri followed Lando Norris by two hundredths of a second on the second hot run, demonstrating McLaren’s speed.
McLaren is doing well since Lando Norris won the Miami Grand Prix.
His potential triumphs have been cost by team and driver error, for which both parties have taken responsibility. On Sunday, he and McLaren will know they must do well.
Norris was quietly pleased with his historic first pole in Hungary and third overall. Although confident, McLaren will also be proud of their recent race progress. No one has won the pole in Budapest since Lewis Hamilton won the race and flag in 2012.
Norris and his crew recognize they must capitalize on closing gaps with 12 races left to drive Verstappen to the finish. Lando Norris understands. Behind Verstappen by 84 championship points.
“I know we missed out on some races, but we did the best we could in every one of them, and I don’t want to get back into all that stuff,” he said. I expect Oscar and Max to challenge me in the rear, not a clean weekend.
“Every location and point must be maximized; the more we can do to return to Max and Red Bull, the better.”
Hungary is a great opportunity since Lando Norris Verstappen was plainly unhappy with his car and outperformed. This disappointed him twice because the team had swiftly upgraded this race.
Verstappen had stated that the upgrades will define the second half of the season, but he admitted that he did not think they had gone far enough and could not defeat the McLarens.
“The changes are effective, but we still need more as we are not at the top,” said he. “Despite the imbalance, I liked the laps. I was pushing hard, so you had these little moments. Fast lap times are less crucial today. Simple: we need to work more because we’re moving slower. McLaren’s qualifying performance suggests a lot of ground to cover.
Lando Norris completed his best lap despite two crash-related stoppages.
Verstappen looked great in dry Q3 hot laps. He set a record with a lap time of 1 minute, 15.555 seconds and was quickest through each sector.
Lando Norris followed and pushed through the corners with fearlessness, posting a perfect 1:15.227 lap time. Piastri improved to second place on the penultimate laps while Verstappen did not, and Yuki Tsunoda’s crash halted the session.
A tardy coda didn’t matter when practice resumed because the last two minutes on old tires were worthless. McLaren has all the cards, but they must perform at the highest level to prove the legendary brand can win again.
Carlos Sainz of Ferrari was fourth and Lewis Hamilton of Mercedes fifth. George Russell, Sainz’s teammate, was unexpectedly ousted in the first round.
Sergio Pérez of Red Bull struggled again in the first qualifying round. He hit the curb, lost the rear at turn eight, and crashed, interrupting the session.
Poor performance again for the Mexican, whose Red Bull berth is in risk after a succession of poor performances, especially in qualification. His contract, recently extended to 2025, may have a performance clause, and Red Bull is unlikely to tolerate him underperforming for long. He was sixteen.
Russell fell behind because Lando Norris Mercedes didn’t fuel the car until the session ended. The British driver was eliminated in 17th place after staying out when the track dried after the break.
Charles Leclerc of Ferrari placed sixth, Fernando Alonso and Lance Stroll of Aston Martin placed seventh and eighth, Daniel Ricciardo of RB placed nine, and Tsunoda placed tenth.
Nico Hülkenberg and Kevin Magnussen of Haas finished 11 and 15, Valtteri Bottas of Sauber 12 and Alex Albon and Logan Sargeant of Williams 13 and 14. Esteban Ocon and Pierre Gasly placed ninth and twentieth for Alpine, while Guanyu Zhou placed eighth for Sauber.
SOURCE: GN
SEE ALSO:
Based on interest from The Range, Homebase’s owner plans to initiate a sale.
Inflation slowed in July, which will lead to 150 bps policy rate cuts, JS Global says.
Police in Chiang Rai Launch Crackdown on Cyber Criminals in Golden Triangle
Automotive
M5 Partially Closed as Cullompton-Exeter Crash Hospitalizes Two
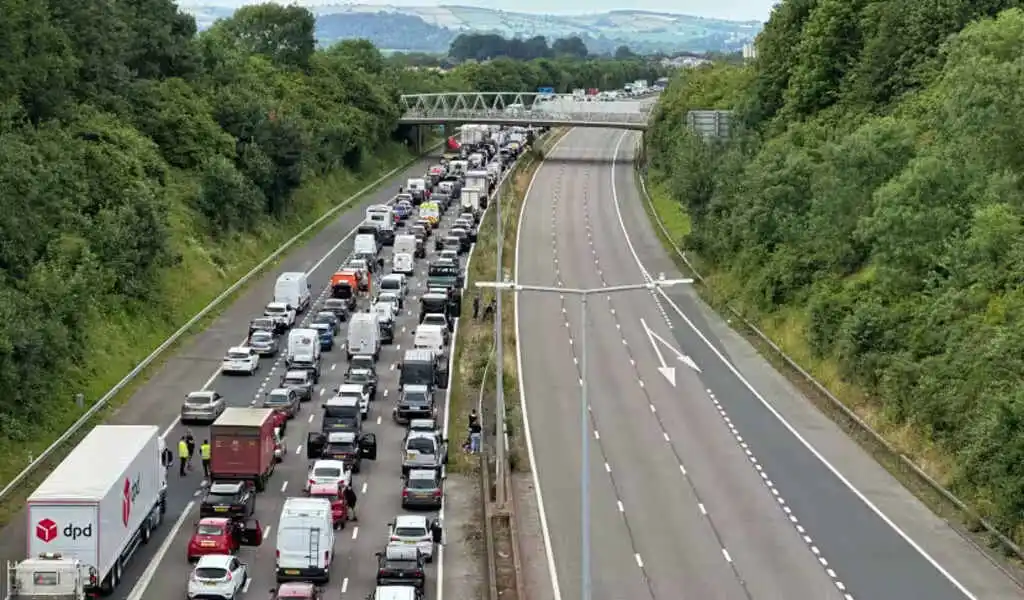
(CTN News) – Two people were sent to the hospital for treatment as a result of the M5 tragic vehicle accident that happened in Devon.
The accident between two vehicles was the cause of the disaster. One more consequence of the crash is that it has left the M5 partially blocked to traffic to this day.
Between junction 28 for Cullompton and junction 29 for Exeter, the highway was blocked in both directions; however, one lane on the southbound carriageway has been opened up for previously closed traffic.
In a statement issued by the South Western Ambulance Service NHS Foundation Trust, they stated that they were notified of a traffic accident that had happened in the Exeter district at 2:29 p.m. on Friday, July 12.
M5 happened in Exeter, according to reports.
Furthermore, information was given to them by the South Western Ambulance Service.
To provide medical assistance to those injured, four land ambulances, each with two crews, an air ambulance, a critical care M5 vehicle, a doctor, an operations officer, and a responding officer were dispatched to the scene of the incident.
Furthermore, a critical care vehicle was dispatched. We also dispatched an air ambulance to the scene of the event.
Two patients were transported to their respective hospitals: one was transported by land ambulance to the Royal Devon and Exeter Hospital, while the second patient was flown there by air ambulance.
After being moved, the two patients were sent to hospitals in Devon and Exeter, respectively. Simultaneously, both patients were transferred to their respective sites at the same time.
Here’s what Devon and Somerset M5 Fire and Rescue Service said:
“We responded to the scene of a road traffic collision on the M5 at 2.30 p.m. today, between junctions 28 and 29.” The statement cited above was part of an official declaration.
A car that had been hit by another car coming from the other direction had two persons inside that had been rescued. It had been traveling in the other direction.
We offered support as the people were being taken out of the car. These people are now receiving medical assistance from the ambulance service in order to fulfill their duties.
The event caused significant delays for the M5 and the routes that pass through Exeter during the period when traffic was being redirected. In order to accommodate the traffic, this was being done.
A southbound vehicle experienced wheel failure, causing it to cross the center reserve and merge with the northbound road approaching. The car was going the wrong way, which is why this happened. The vehicle was traveling southward at that precise moment.
National Highways indicated that based on the facts they have provided, it is expected that the police would begin their investigation into the occurrence given the magnitude of the calamity that occurred. The entity that made this information public was National Highways.
The Devon and Cornwall Police Department issued the following statement:
“We know the M5 closure is causing traffic.”
The statement that was released is located beneath you. “We will get people moving safely when we can but please bear with us while we deal with the incident and causalities at the scene.”
In order to accommodate cars and other small vehicles that were traveling on the now-closed northern route towards M5 Taunton and Bristol, the back of the line has been shifted.
This was done to create space for these cars, which were heading towards Taunton and Bristol. The purpose of this activity was to provide space for larger cars. At this point, it seems like more and more vehicles are being stopped from going forward.
Due to this incident, a second lane has been opened up for use by any and all vehicles traveling southward.
SOURCE: ITV
SEE ALSO:
Honda to Cease Production at One of its Thailand Auto Factories
Car Dealers in Northern Thailand Struggling to Stay Afloat
BYD Car Buyers in Thailand Outraged Over Huge Dealer Discounts
Automotive
Honda to Cease Production at One of its Thailand Auto Factories
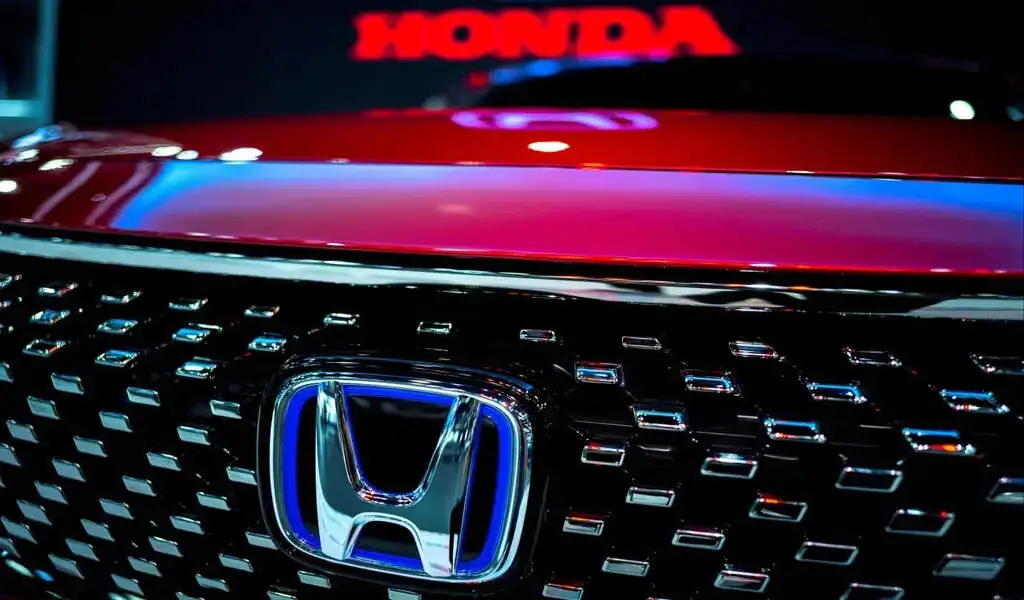
(CTN News) – The Japanese vehicle firm Honda Motor made the news in a statement that was posted on Tuesday. The statement stated that the company intends to center its production at the site that it operates in the province of Prachinburi.
As a consequence of this, the production of automobiles will be halted at the facility that it operates in the province of Ayutthaya in Thailand by the year 2025.
The more difficult circumstances that the second-largest car manufacturer in Japan is facing in the country of Thailand, which is located in Eastern Southeast Asia, are exemplified by this move. Thailand is located in Southeast Asia.
There are several reasons for this, including the fact that Chinese firms are determined to grow their market share in Thailand, and a growing number of consumers are expressing an interest in electric vehicles (EVs). They both play a role in contributing to the problem.
The combined output of automobiles produced by Honda’s two facilities has fallen throughout the course of the succeeding four years, going from 228,000 vehicles in 2019 to less than 150,000 vehicles annually. This downward trend has occurred during the course of the past four years.
The preceding four years have been the time period during which this decline has taken place. With regard to the sales that the company has made in Thailand throughout the course of the past four years, there has been a consistent range of less than 100,000 to less than 100,000 for the entirety of this time period.
This is according to Honda’s spokeswoman.
When the factory first opened its doors in 1996, the company anticipates that it would continue to manufacture vehicle components at that location. When the firm finishes manufacturing vehicles at the Ayutthaya facility in the next year, the spokesperson stated that the company intends to continue producing automobile components at the plant.
In accordance with the statement that was given by the spokesman, the Prachinburi factory, which was built in 2016, will be utilized for the purpose of integrating the facilities with which automobiles are created. This was said in the statement. There are only two factories in Thailand that are owned and operated by the vehicle manufacturer, and these two factories are the only ones in the country.
According to the statement made by a spokeswoman for Honda in Thailand, the company’s goal is to reduce the disparity between the number of automobiles it produces and the number of sales it has experienced in the nation.
According to the remark that was made by the spokesman for the company, the automobile manufacturer are already exporting their products from Thailand, particularly to other Southeast Asian countries such as Indonesia and the Philippines. According to a statement that was sent by a spokeswoman for the company.
Currently, Honda has no plans to invest in Thailand.
When it comes to mainland China, Honda and Nissan Motor, a Japanese automobile manufacturer that competes with Honda, have been hit particularly hard by competition from rising Chinese manufacturers.
Nissan Motor is a competitor of Honda. As a result of the fact that these businesses provide reasonably priced plug-in hybrids and electric vehicles that are loaded with software, a significant number of customers have been drawn to them.
Now, Japanese automobile manufacturers are at risk of losing clients in countries outside of China, such as those in Southeast Asia, to Chinese companies that are increasingly attempting to increase the quantity of automobiles they export and build up operations outside of China.
As a result, Honda Japanese automobile manufacturers are facing a potential loss of customers. They are exposed to this danger as a result of the fact that Japanese brands compete with Chinese brands in these locations.
BYD, a Chinese manufacturer of electric vehicles, recently launched a plant in Thailand that will be responsible for the production of automobiles that are powered by electronic batteries.
This plant was established last week. The Chinese electric car manufacturers are beginning to establish facilities in the country, and this factory is a component of the wave of investments that they are making in the country. These investments have a total value that is greater than 1.44 billion dollars together.
SOURCE |SCMP
SEE ALSO:
Car Dealers in Northern Thailand Struggling to Stay Afloat
BYD Car Buyers in Thailand Outraged Over Huge Dealer Discounts
The PM Seeks Assurances after BYD’s Steep EV Discounting in Thailand Sparked Backlash
-
News3 years ago
Let’s Know About Ultra High Net Worth Individual
-
Entertainment2 years ago
Mabelle Prior: The Voice of Hope, Resilience, and Diversity Inspiring Generations
-
Health3 years ago
How Much Ivermectin Should You Take?
-
Tech2 years ago
Top Forex Brokers of 2023: Reviews and Analysis for Successful Trading
-
Lifestyles2 years ago
Aries Soulmate Signs
-
Movies2 years ago
What Should I Do If Disney Plus Keeps Logging Me Out of TV?
-
Health3 years ago
Can I Buy Ivermectin Without A Prescription in the USA?
-
Learning2 years ago
Virtual Numbers: What Are They For?